|
1.Drawbacks of a conventional shuttle loom |
In conventional looms, a shuttle housing a pirn of weft yarn is propelled to-and-fro across warp shed by either an overpick or an underpick shuttle propulsion mechanism. Such a system suffers from the following drawbacks.
|
- A large shuttle mass of about 450g (for cotton weft yarn) is employed for transporting a pick of weft which is about 0.2 g/m on the average, leading to a considerable waste of energy
- Unguided free flight of shuttle can lead to shuttle fly, abrasive damage of reed and shuttle as also uncontrolled weft tension.
- Shuttle checking within the confined space of a shuttle box results out of multiple impacts. Consequently the exact location of rest position of shuttle within a box becomes indeterminate, affecting efficient transfer of picking energy during acceleration of shuttle. Moreover such impacts result in damage to shuttle and pirn.
- Mass of shuttle with full pirn and with near empty pirn can differ by about 10%. As a result the nature of shuttle flight varies in a periodic manner which in turn affects weft tension profile and therefore properties of the resultant fabric.
- Noise emanating from weft insertion systems employing a conventional shuttle can be as high as 110dB
- Shuttle is made of an assembly of various elements which may come apart over a period of time due to multiple and severe impactual cyclic loads. Moreover the major component of shuttle is good wood which is becoming scarce by the day.
- Limited space within shuttle limits pirn size which leads to frequent pirn changing. This is a source of additional workload and frequent defects. A plain loom stops running when a pirn is exhausted. Restarting the loom with a new pirn invariably causes a starting mark in fabric while imposing a periodic workload on loom operator. On a pirn changing loom one needs an additional worker in the form of battery filler. Unintended pirn mixing is a frequently encountered problem during battery filling. Moreover faulty working of the pirn changing motion very commonly results in lashing-in problem.
- While a shuttle is in state of rest within a shuttle box, the weft thread that it carries in the pirn extends from the instantaneous unwinding point on the pirn body, passing through the shuttle eye and ending up at the fabric selvedge. It is observed from Fig 1 that due to asymmetric location of shuttle eye on the shuttle body, length of this thread segment is higher when the shuttle is in the right hand box than when it is in the other. Thus as the shuttle is accelerated from its state of rest in a shuttle box, the weft thread initially falls slack and remains in such a condition till the shuttle has travelled a fair distance into the shed to have completely taken up this slack. Evidently the distance that the shuttle has to travel before the weft thread can become taut again is higher in alternate picks than in the intervening ones. During the subsequent displacement of shuttle, weft unwinding rate would depend to a large extent on the flight trajectory of shuttle as one end of the weft remains firmly anchored to the stationary fabric selvedge while the three dimensional coordinates of shuttle eye undergoes a continuous change. Over and above, the effect of the fourth dimension, i.e. time also plays a role as the flight velocity varies with continuously changing combined mass of shuttle and the depleting pirn. As yarn tension depends on its unwinding rate it is evident that weft tension even during this phase of shuttle flight would keep on varying from one instant to other. Superimposed on this tension variation would be the effect of variation of unwinding point on the pirn itself. Finally as and when the shuttle enters the deceleration phase, multiple impacts would cause further uncontrolled and indeterminate changes in tension in the inserted pick of weft, which during this phase still lies untrapped and free within the warp shed. Thus at the end of a picking cycle with a conventional shuttle, a curvilinear segment of thread lies stretched across the warp shed in an undefined and non-uniform state of tension. During the subsequent phase of shed change and beating up process a heterogeneous crimp distribution between warp and weft threads across the fabric width would be the logical consequence. This effect viewed over a series of consecutive picks leads to very non-homogeneous woven fabric, as crimps in warp and weft threads and their homogeneity primarily governs properties of woven fabrics.
|
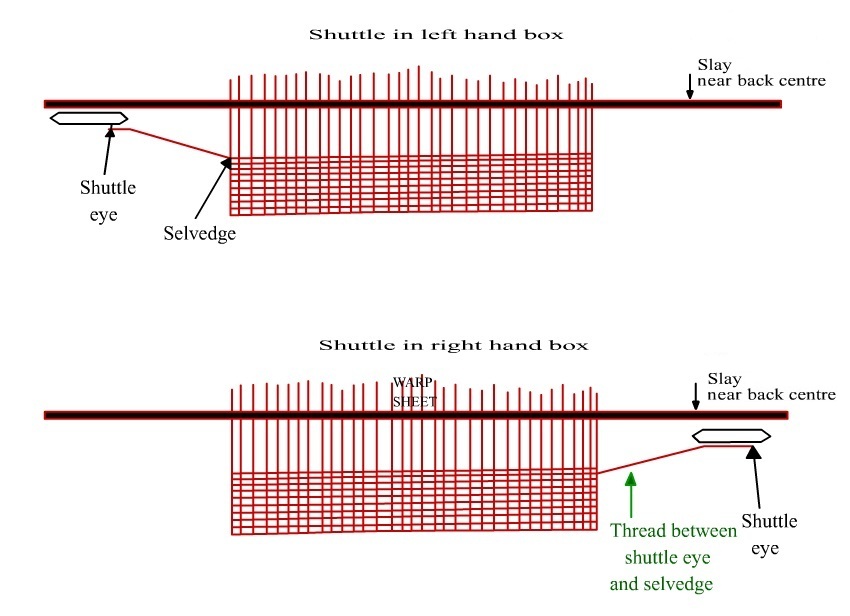 |
Fig. 1 |
|
Observing that (Appendix I) power consumed by shuttle during its acceleration phase is proportional to the product of its mass and (loom rpm)3, it is evident that a lowering of shuttle mass can be translated into higher loom speed and hence higher loom productivity. Moreover smooth passage of a large shuttle through the confined space within a warp shed and over a large reed width demands a high sweep as also high eccentricity of sley, factors that adversely affect loom speed. Hence a reduction in mass and dimensions of shuttle provides an efficient route to raising loom productivity. Mass of a conventional shuttle can be reduced by reducing its dimensions and by opting for a lighter and stronger material. The first option would aggravate problems related to pirn changing while the second solution has not found any commercial acceptance. An elegant solution to this vexing issue is found in the unconventional, i.e. the so called Shuttleless weft insertion systems.
|
|
|
|
|
|
|
Copyright IIT Delhi © 2009-2011. All rights reserved. |
|